JUST-IN-TIME LOGISTIC SERVICES
This system allows the optimisation of product deliveries to an end customer just in time and at the right place in the production sequence.
It consists in the continuous monitoring of the customer’s needs in terms of the range and number of required products. Fasteners are delivered directly to a production/assembly line without engaging the customer’s own staff in the process of the planning and executing of purchases, storing, and without tying up funds in warehoused stocks.
Benefits of implementing the Kanban system:
- Elimination of inventories – products are delivered in module quantities, adjusted to the current production size.
- Reduction of the warehouse space and the elimination of the time required to collect details from a warehouse – items are delivered directly to assembly lines. The system of deliveries does not require warehousing, or services relating to the receipt and issue of goods from the warehouse.
- Reduction of costs relating to purchases – analysis of warehoused volumes, preparation of orders – the use of fasteners is monitored directly at the customer’s assembly line and this triggers subsequent deliveries.
- Provision of deliveries of fasteners to a team with dozens of years of experience in deliveries made directly to assembly lines.
Why Asmet?
Multi-year experience
Our biggest advantage is experience in the implementation and execution of deliveries using the Kanban system (JiT).
Our references are customers with whom we launched the first deliveries directly to assembly lines over 15 years ago, and who have stayed with us until today. Together, we improve logistics solutions, employ new tools and methods, and adjust to new requirements. At present, we provide support to several dozen companies (in Poland and abroad) of different sizes and in different industries.
Individual customer approach
In view of high differentiation in terms of process organisation, while implementing Kanban systems our engineers do not impose out-of-box models, but always collaborate with the customer to develop an individually tailored solution, which both takes into consideration its expectations and offers any additional functionalities required by the customer. Service process optimisation is performed on the basis of a systemic analysis of data and tests, the results of which are always discussed with the customers. That is why we can ensure that the designed support system reflects the real needs of the users of our solutions.
Innovation
At Asmet, we place great emphasis on the continuous improvement of processes and the search for innovative organisational and technical solutions that enhance the efficiency of processing orders.
So as to meet the increasing demands of our customers, we have implemented a transparent web application for placing orders. We have also made its mobile version available (running on Android), which is used for scanning Kanban cards. For foreign customers we offer all applications in English.
Apart from software tools, our solutions also offer other elements of the infrastructure necessary for the operation of the Just-in-Time system, including mobile racks, code readers, and KLT containers.
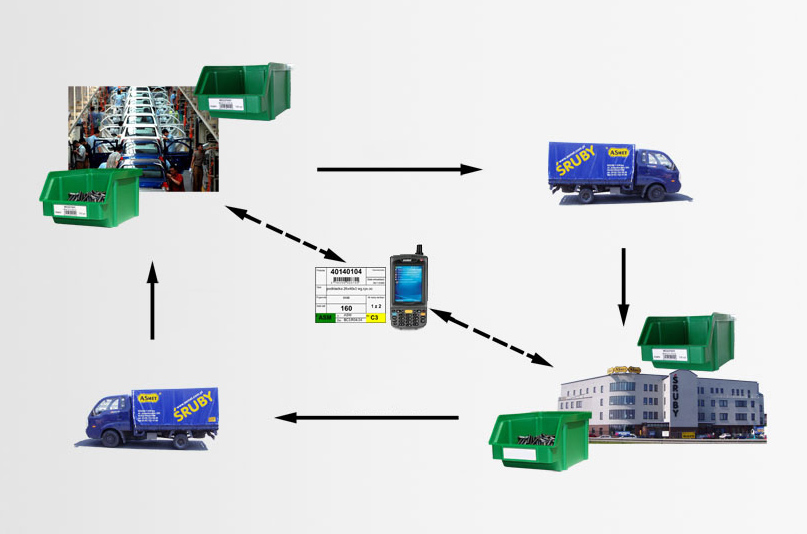
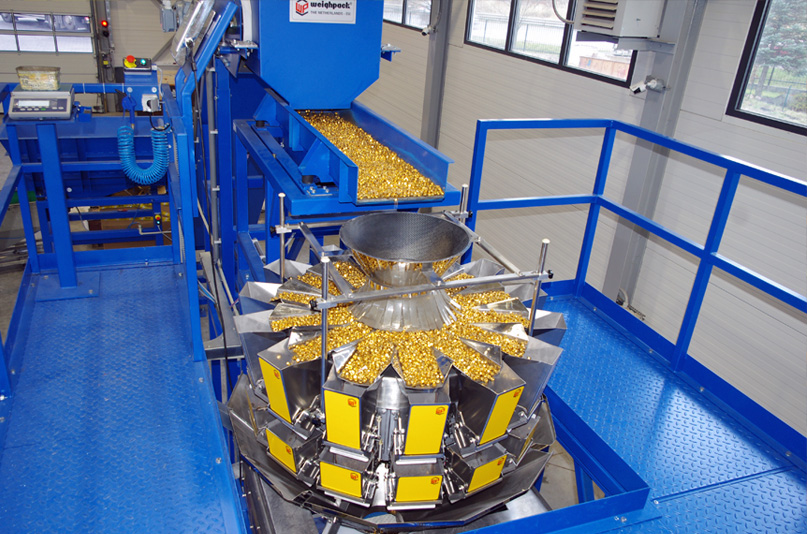
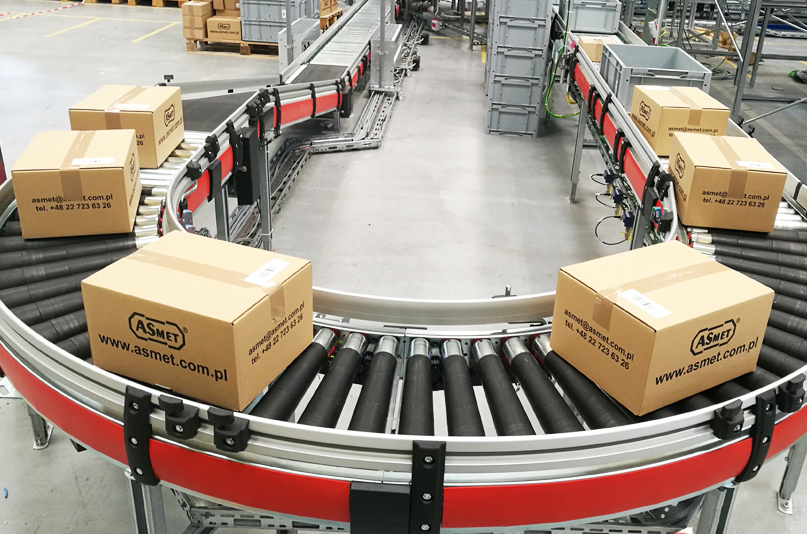